在制造領域,復雜零件的加工精度與效率一直是衡量技術實力的核心指標。傳統加工方式常因設備限制,需多次裝夾、多工序切換,導致加工周期冗長、精度波動大。而龍門五面加工中心憑借其五軸聯動技術,以“一次裝夾、五面加工”的革新理念,正重新定義復雜零件的制造標準,為航空航天、汽車制造、精密模具等行業帶來變革。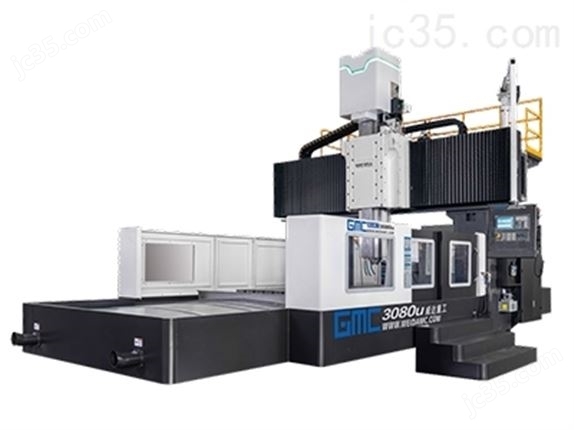
五軸聯動:突破傳統加工的維度局限
傳統三軸加工受限于平面運動軌跡,難以高效處理復雜曲面、深腔結構或異形零件。而龍門五面加工中心通過A/C軸旋轉與X/Y/Z軸直線運動的協同配合,可實現空間內任意角度的刀具路徑規劃。例如,在航空發動機葉片加工中,五軸聯動技術能精準貼合葉片的復雜型面,避免傳統工藝中因多次裝夾導致的累積誤差,將加工精度提升至微米級。這種多維度的加工能力,不僅提升了零件的幾何精度,更保障了其動態性能與使用壽命。
高效集成:一次裝夾,五面加工
傳統加工方式需多次拆裝工件以完成不同面的加工,這不僅增加了操作復雜度,更易因定位基準變化導致尺寸偏差。加工中心通過集成式設計,可在一次裝夾中完成零件五個面的加工,大幅縮短加工周期。以汽車模具制造為例,傳統工藝需數天完成的型腔加工,五面加工中心僅需數小時即可完成,且表面質量更優。這種效率提升不僅降低了生產成本,更滿足了制造對快速響應與精益生產的需求。
重載穩定:支撐高精度加工的基石
復雜零件加工往往伴隨高切削力與振動,這對機床的剛性與穩定性提出嚴苛要求。加工中心采用龍門框架結構與高精度線性導軌,配合大功率主軸與動態平衡系統,可承受高負載切削,同時保持亞微米級定位精度。例如,在鈦合金零件加工中,設備能以高速切削去除大量材料,同時通過熱補償技術抑制熱變形,確保零件尺寸一致性。這種“剛柔并濟”的設計理念,使其成為高硬度材料加工的理想選擇。
智能化賦能:從經驗驅動到數據決策
現代龍門五面加工中心已融入智能化控制系統,通過實時監測刀具磨損、切削力變化等參數,自動調整加工策略。例如,設備可基于AI算法預測刀具壽命,提前規劃換刀路徑,避免非計劃停機。此外,虛擬仿真技術可預先驗證加工路徑,減少試錯成本。這種數據驅動的制造模式,不僅提升了生產效率,更推動了從“經驗加工”向“智慧制造”的轉型。
應用拓展:制造到通用領域
五軸聯動技術的普及,使加工中心的應用邊界不斷延伸。除航空航天、汽車等傳統領域外,其在醫療器械、新能源電池、3C電子等領域同樣表現優。例如,在人工關節加工中,設備能以納米級精度塑造關節曲面;在電池極片生產中,五面加工可實現極耳與極片的一體化成型,提升電池能量密度。
從精密模具到大型結構件,從實驗室研發到工業化量產,龍門五面加工中心正以五軸聯動技術為核心,推動復雜零件加工向高效、高精度、智能化方向演進。未來,隨著材料科學與智能控制的進一步融合,這一設備必將在更多領域釋放潛力,成為制造的“儀器”。